
The second setting position errors by measuring values will be replaced using the PI as follows: 7μm. software a digital control system to regulate the parameters Kpos, Gain Ki, and Gain Kp. (propotional, and integrative) system using the PI-Fuzzy Logic Controller method. Lubis Electrical Engineering Departement, functions to produce good quality of production and precision.

1022–1033, Article ID: IJMET_09_12_102 0976-6359 Scopus Indexed ANALYSIS OF SERVO CONTROL SYSTEM METHOD Riny Alfina Student of Electrical Engineering Departement Nasril Tanggerang Selatan, Indonesia i Danny M. The results of error the position of hydraulic system obtained using the PI system a method as follows: 1.31μm Key words: Hydraulic Controller. The PI parameter Controller method to compare with the PI system whether the graph values are the same as equal to 10 microns or otherwise. To solve these problems, there are two setting used, first of the control system including Gain used the PI-Fuzzy Logic Controller method to minimize PI parameters. There are some problems in industries regarding servo hydraulic control system positioning due to its functio This research was focused on two cases, firstly analysis of commercially developed hydraulic servo system, secondly optimization of PI parameters of the hydraulic servo Mainly, final goal of this research is a optimization and minimization the position of the hydraulic servo system to be less than 10 microns. Results in this paper shows that the proposed fuzzy based control approach produces faster speed response with very less rise time and settling time as compared to the conventional PI controller. The fuzzy controller is compared with conventional PI controller for speed response. In this paper, MATLAB/Simulink model is designed and developed for fuzzy Logic based speed control of PMDC motor. Considering such a wide range of applications of PMDC motors, the proposed fuzzy logic-based speed control approach will be more convenient as compared to the traditional PI (Proportional-Integral) based speed control technique. Also, PMDC motors are used for auxiliary application purposes in industry, e.g., cranes, air compressors, blowers and lifts.
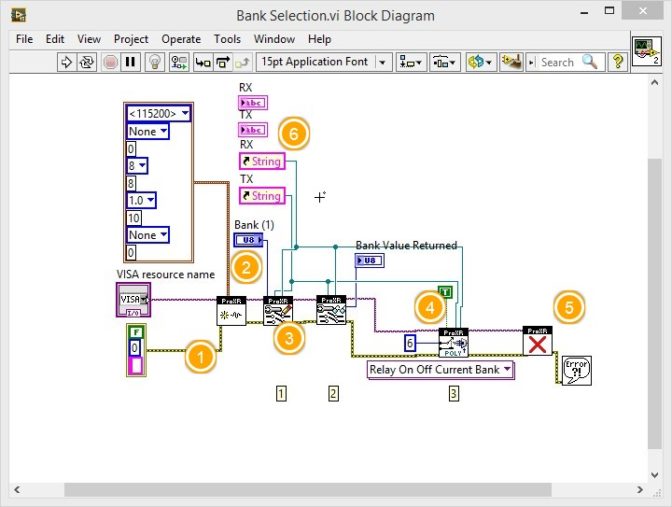

It has constant speed from no load to full load, higher energy density and simplicity in construction which opens a wide range of household uses such as hair drier, vacuum cleaner, fans and sewing machines. Permanent Magnet Direct Current (PMDC) brushed motors are widely used in various industrial applications like drills, boring mills, lathe machines, spinning and weaving machines.
